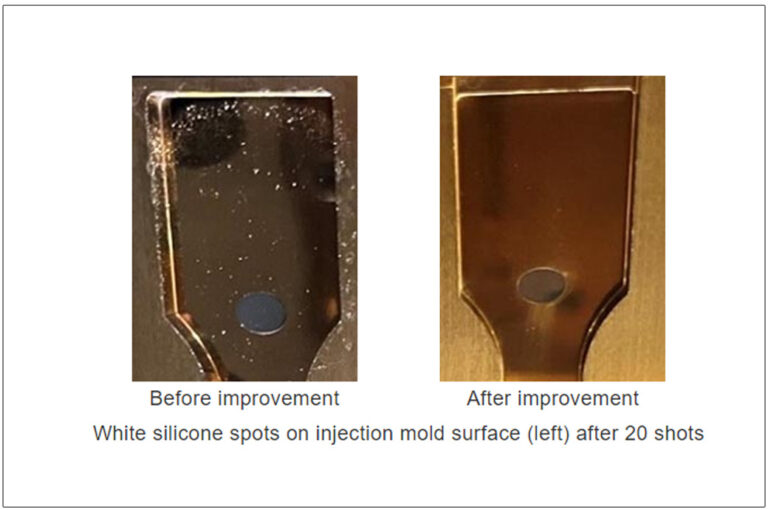
[ad_1]
The company created this product by combining particular additives with resin that Refinverse group, recycled by stripping silicone from airbag fabric scrap cuttings. and thereafter washed. The new offering will debut as Ecouse AMILAN. Toray looks for that offering to accelerate the expansion of Ecouse (pronounced Eco-Use), a proprietary integrated brand for eco-friendly recycled materials and products that it rolled out worldwide in 2015, the company said in a press release.
Japan’s Toray has made recycled nylon 66 recovered from silicone-coated airbag fabric scrap cuttings. This material achieves the same flowability and mechanical properties as injection moulding grades from virgin nylon 66. Toray specialises in industrial products centred on technologies in organic synthetic chemistry, polymer chemistry, and biochemistry.
The nylon 66 fabric of airbags can be silicone-coated or non-coated. Manufacturers normally recycle the scrap cuttings of non-coated fabrics. Recycling coated airbag fabric scrap cuttings requires removing the silicone. Refinverse was the first in Japan to achieve commercial-scale silicone-coated fabric recycling. Recycling through stripping and washing has typically left silicone traces, however, degrading the resin and contaminating moulds during injection moulding. Another issue has been that the high viscosity of airbag yarn limits applications in thin-wall and other injection moulding processes in which high fluidity is vital.
Toray accordingly combined particular additives so residual silicone resin would not migrate to the surface of moulded products. It also greatly reduced mould adhesion. That is why the flowability and mechanical properties of recycled nylon 66 with Toray’s technique are on par with those of virgin nylon 66. Toray plans to start full-fledged sample work in April 2023 or later. It ultimately looks to procure recycled raw materials at its overseas sites to establish a global supply system. It will also explore commercialising recycled nylon 66 products made from airbags recovered from end-of-life vehicles.
The company has cultivated recycled plastic products derived primarily from post-industrial scrap materials from in-house production processes, undertaking such efforts as recycling used air conditioner parts into new ones. It aims to extend recycling to used automotive parts and industrial equipment.
Toray intends to launch Ecouse Toraycon as a chemically-recycled polybutylene terephthalate resin product that has properties equivalent to virgin materials. It will keep assessing material recycling and chemical recycling for its own polymers in driving to expand the Ecouse line-up by bringing out such products as Ecouse Toyolac acrylonitrile butadiene styrene, Ecouse Torelina polyphenylene sulfide.
Fibre2Fashion News Desk (GK)
[ad_2]
Source link